For years, the simple mantra for making a winning car in Formula 1 (and other race categories) was to add more bhp to the engine. A powerful engine meant more speed and that was the focus of every engine supplier.
Not surprisingly, the F1 car engines in the 1980s were belting out close to 1000 horses. In contrast, the F1 cars of today have a smaller engine capacity and less power, yet they are breaking the circuit records with ease.
Whats the reason behind this?
Thanks to aerodynamics and cutting-edge design technologies, cars of today move much more efficiently on the track, utilizing the airflow in a way that reduces drag while creating enough downforce to negotiate the corners at previously unimaginable speeds. A key component of the technology that has made this possible is CFD or Computational Fluid Dynamics.
Computational fluid dynamics (CFD) is the use of applied mathematics, physics and computational software to visualize how a gas or liquid flows, interacts with and affect the objects as it flows past.
In the case of automobiles (and aircrafts and projectiles), CFD is used to predict the airflow around the car as it moves and corners at different speeds and conditions, temperatures and pressure fields that act on the car as well as the resultant downforce and drag experienced.
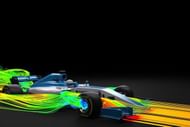
Traditionally, new car designs have been tested for aerodynamic performance in a wind tunnel facility. This involves creating a scale model of the car and passing air over it simulating a real track scenario.
The air can be smoked (or dyed) so that its movement and interaction with the car is visible. However, the wind tunnel approach requires infrastructure, building of very accurate models and even a small design change. Testing requires a new scale model altogether.
This is where CFD comes to the rescue. It can do all of this using a computer. In fact, it can run numerous simulations per day at a fraction of the cost involved in wind tunnel testing.
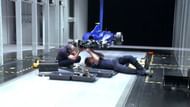
How effective is CFD? In one word: Very. With many teams sharing the same engines/power units, aerodynamics automatically become the differentiating factor. CFD has enabled even the smaller teams (in terms of budget and facilities) to harness the power of aerodynamics, which according to experts, contribute up to 80% of the car’s on-track performance.
In fact, the VR-01 car fielded by Virgin Racing in the 2010 season and the MVR-02 used by Marussia Virgin Racing in 2011 were designed entirely using CFD with no wind tunnel testing involved.
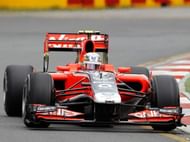
How CFD is already impacting the race business:
1. Reducing the Entry Barrier: For many prospects, the cost involved in fielding an F1 team is way too high to consider an entry. CFD brings down a significant portion of the costs involved in designing and testing.
2. Green Impact: With F1 investors committed to making the sport greener, CFD reduces the environmental impact to some extent by cutting down the number of physical trials that require dedicated facilities and energy. Also, by making cars more efficient, their carbon footprint is reduced.
Are wind tunnels still relevant? As of now, very much. CFD and wind tunnels can be viewed as two uncompromisable components of car design. Both should work in tandem and complement one another.
The reason that wind tunnels are here to stay is the need of validation. Quite often, it has been observed that the results obtained from CFD testing do not match with the data when the same design is tested in a wind tunnel.
Furthermore, when the car hits the track, the results can be completely off the mark. Clearly, the team with the highest correlation between results of wind tunnel testing and CFD simulations takes the pie.
The Future: CFD is a powerful and fast-evolving tool which is getting better with each passing year. While there are still a few limitations involved, as F1 gravitates towards a greener, leaner and more cost effective future, CFD will be the key to success.