Do robots and metrology matter more now than ever before in NASCAR's single-source supplier age? Hendrick Motorsports (HMS) Vice President of Competition Chad Knaus recently opened up about innovation in the Rick Hendrick-owned auto racing team.
NASCAR’s Next Gen regulations standardize roughly 85% of the car’s build. Hendrick Motorsports uses a stack of scanners, simulation tools, and robotic arms to extract every thousandth that remains on the table.
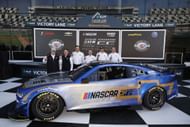
Every team receives the same parts from the same suppliers and is required to run them as delivered, which includes wheels (BBS), tires (Goodyear), brakes (AP Racing), to prop shafts (Lentus), anti-roll bars (Roush Yates), and the chassis itself (Technique). However, the remaining 15% is open to innovation in the assembly process, like fitment, tolerance stacking, and integration.
And Hendrick Motorsports has turned that margin into its competitive edge, believes HMS competition VP Chad Knaus, who spoke to Motorsport about this.
“They (NASCAR) want to have a set of tolerances that everybody has to operate within and it is up to us (teams) to take those tolerances, stack them up in a way that creates performance. Whatever that metric may be that we determine is the most important performance enhancer for that track and apply it. "
He added:
"Whether that be weight, whether that be geometry, whether that be shape. There’s a million ways to do that and each race track is unique in which one you need to apply or how you need to apply it and we do that with all of this Hexagon equipment that we’re very fortunate to have.”
Knaus also mentioned during the interview that at the heart of HMS' operations sit the 33 Hexagon Absolute Arms, 13 laser scanners, and 7 coordinate-measuring machines (CMMs) spread across the Hendrick campus. The team’s new metrology lab was built in collaboration with Hexagon back in 2016.
The lab gives them the ability to build an entire car in virtual space and then validate its real-world version. It's here where HMS follows a rigorous procedure where race cars are not assembled but engineered like spacecraft.
HMS’ high-tech build process, the reason behind their NASCAR success
NASCAR's intention behind locking 85% of the Next Gen car's build was to bring parity and close the gap in the field. Teams like Hendrick Motorsports are using the same raw materials as their rivals but are winning by being exponentially better at how they use them.
HMS' Hexagon Tempo robotic cells load parts into scanning stations. Here, Touch+ coordinate-measuring machines (CMMs) and laser scanners map each part’s surface geometry. Each piece is automatically scanned, probed, tagged by serial number, and entered into a central database. The data then feeds HMS’ simulation software, allowing engineers to virtually build cars before a single bolt is torqued.
The Absolute Arms then allow HMS to scan primary chassis pieces. This includes all seven center sections, ten front clips, and ten rear clips per car number and assemble a map of potential geometries.
Roy Crump, Hendrick Motorsports' quality control supervisor, talked about the recent delivery of new Hexagon systems that prompted a re-measurement of every existing part in the inventory. He said to Motorsport:
"For the last two or three months, we have been trying to measure as many parts as we can just to verify what we have because like I said, in the past we were using two guys to measure with the Romer arms. So, re-measuring everything we have in our inventory."
The work put in by Hendrick’s shop is visible on Sundays, as the team has had a strong start to the 2025 season. HMS has found two victories and eight top-five finishes so far in the 2025 NASCAR Cup Series, with all four cars fielded by the 50-year-old team currently in the top five of the Cup standings.
Get the latest NASCAR All-Star race news, Xfinity Series updates, breaking news, rumors, and today’s top stories with the latest news on NASCAR.